Gas to Hydrogen Plant Details
Overview of the Gas-to-Hydrogen (GTH) Process
Greenway Technologies (GWTI) offers a state-of-the-art Gas-to-Hydrogen (GTH) plant solution that converts natural gas into high-purity hydrogen. This advanced technology leverages the hydrogen-specific version of the G-Reformer®, the H-Reformer® system, to produce hydrogen efficiently while ensuring environmental sustainability.
Key Requirements
To operate a GTH plant, several critical inputs are required:
- Pipeline-Quality Natural Gas: The plant can utilize natural gas from pipelines, commercial gas supplies, renewable sources, or directly from gas wells with adequate gas quality. The H-Reformer® continuously monitors the composition of input gas in real-time to ensure optimal operation. Non-commercial gas sources may require additional pre-treatment if sulfurous compounds or other contaminants exceed system limits. A certified fuel sample analysis is recommended to assess gas suitability and potential efficiency improvements when “non-pipeline” gas is used.
- Oxygen (O₂): The process requires oxygen with a purity of 90%. For single G-Reformer® systems, local liquid oxygen (LOX) deliveries can eliminate the need for on-site oxygen concentration. For larger plants with multiple H-Reformers®, an on-site oxygen-concentration plant is necessary. Various oxygen-concentration technologies are available, becoming more cost-effective as plant size increases.
- Clean Water: Essential for the hydrogen production process.
- Electricity: Required to power the GTH plant operations. Options exist to co-generate electricity where grid power is unavailable.
System Operation and Control
- The H-Reformer® is operated using a custom-built control panel from GWTI. This control panel provides local or remote monitoring and control capabilities, enabling real-time system performance oversight. The control console is equipped with logic to monitor natural gas input composition and manage all aspects of the H-Reformer® operation. In case of any issues, the system can initiate actions such as shutting down the H-Reformer® if necessary. System modifications can be input as commands via the control panel. An example would be allowing overall hydrogen production to be varied from 50%-100% of H-Reformer® system capacity. This feature may be extremely useful in production situations where specific quantities of hydrogen are required, such as electrical generation.
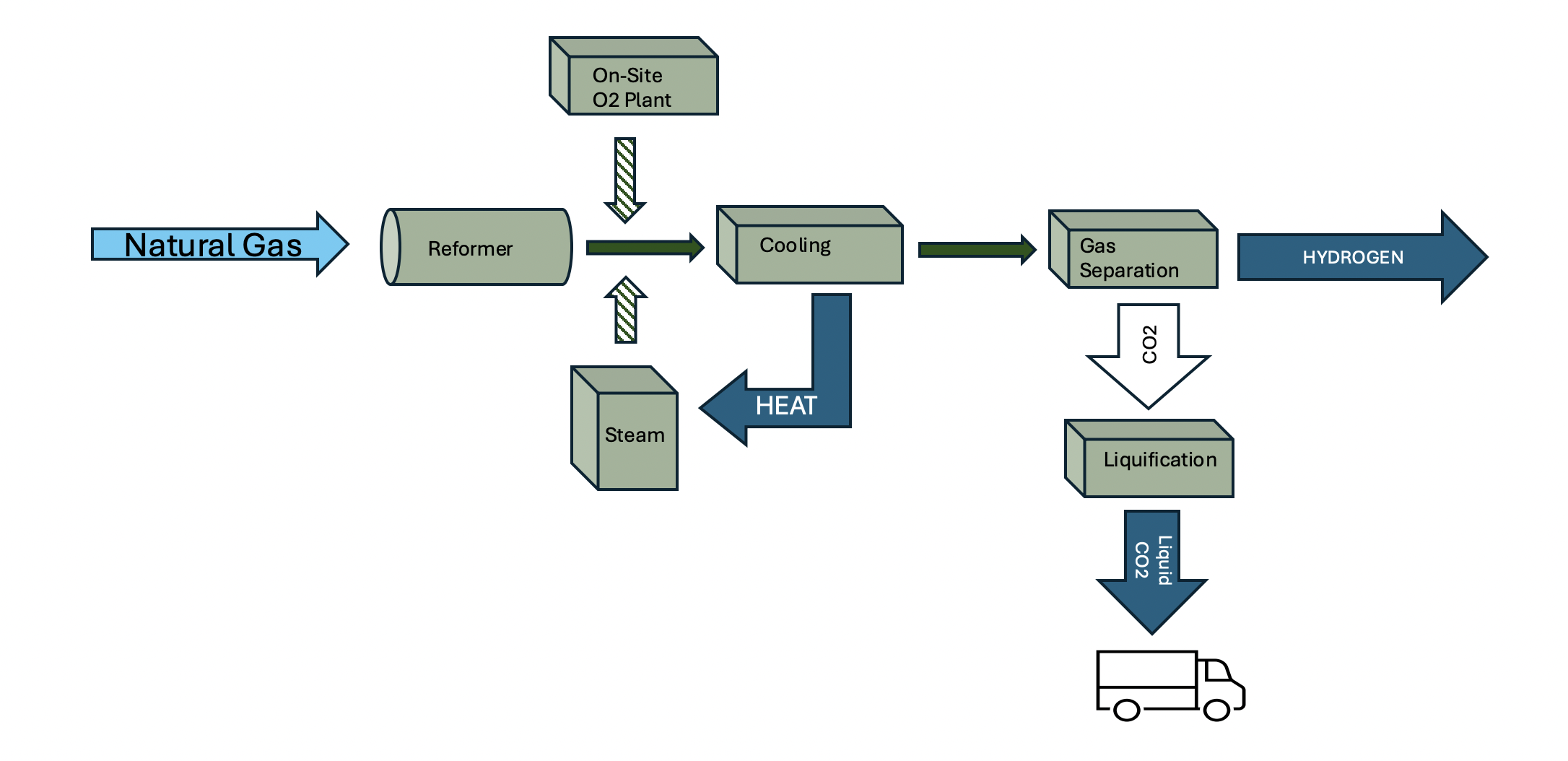
Hydrogen Production Process
- Initial Reforming Stage: The H-Reformer® begins by converting natural gas, oxygen, and steam into a mixture of hydrogen, carbon dioxide, and carbon monoxide. This step utilizes different operational parameters from those of the original G-Reformer®.
- Catalyst Stage: A catalyst is introduced to increase hydrogen production and convert residual carbon monoxide into carbon dioxide. This stage is specific to the GTH H-Reformer® process and is not used in other G-Reformer® applications. The method utilizes the remaining heat for this conversion. The result is highly energy-efficient and low carbon emission conversion free of any “heating gas,” as used in alternate hydrogen conversion processes.
- Liquefaction: Output is sent directly to a separation system where carbon dioxide (CO₂) is liquefied under specific conditions and separated from the hydrogen. The liquid CO₂ is transferred to tanker trucks or rail cars for sequestration or sale. Local conditions may present opportunities for selling CO₂ for various uses.
- Hydrogen Output: The final hydrogen product exits the plant at low pressure, slightly above atmospheric pressure, ready for distribution or further use. Processes such as electrical generation can use hydrogen at this output pressure. An optional plant feature involves hydrogen compression for uses that require it, such as vehicle use or storage.
Environmental and Economic Benefits:
-
The GTH process is relatively small, allowing the creation of hydrogen at virtually any site with a natural gas source. This eliminates the expensive liquefaction and transportation of conventionally created hydrogen to an end site. The H-Reformer® is exothermic (heat producing), making the gas conversion extremely efficient and allowing for a low cost of production. Since virtually all carbon generated is captured, hydrogen created with “fossil” natural gas will be defined as “blue” hydrogen. Inputting “renewable” natural gas will result in “green” hydrogen. Clean air credits may be available for these grades of hydrogen, further enhancing the plant’s economic benefits.