Gas to Liquid Plant Details
Overview of the Gas to Liquid (GTL) Process
A Gas-to-Liquid (GTL) plant requires several vital inputs, including pipeline-quality natural gas, 90% purity oxygen (O2), clean water, and electricity. Since each site has unique characteristics, conducting a site survey by an EPC (Engineering, Procurement, and Construction) firm is a recommended first step once serious interest in constructing a GTL plant has been established.
Key Requirements:
- Pipeline Quality Natural Gas: The natural gas supply can come from various sources, such as a pipeline, a commercial gas supplier, a renewable gas source, or directly from a gas well, provided the gas meets specified quality standards. The G-Reformer® console continuously monitors the composition of the input gas in real-time, which is especially critical for non-commercial gas sources. Pre-treatment of “well-head gas” may not be necessary if the gas falls within the acceptable range for sulfur compounds as found in commercial natural gas. For well-head gas, a certified fuel sample analysis is crucial to determine its suitability, and in some cases, more energetic gases can enhance production efficiency.
- Oxygen:The plant requires 90% purity oxygen. For a single G-Reformer® system, liquid oxygen (LOX) can be delivered from a local supplier, eliminating the need for on-site oxygen generation. However, an oxygen-concentration plant will be necessary for larger plants (more than one G-Reformer®). Various oxygen concentration technologies are available, which tend to become more economically efficient as plant size increases.
- Clean Water: Essential for the production process.
- Electricity: Required to power the GTH plant operations. Options exist to co-generate electricity where grid power is unavailable.
System Operation and Control
- The G-Reformer® system is controlled via a custom-built control console developed by GWTI. This console allows for remote monitoring and control, including monitoring natural gas input composition and taking autonomous action, such as shutting down the system if necessary. In its initial stage, the G-Reformer® produces a mixture of hydrogen and carbon monoxide, known as SYNGAS. This SYNGAS is carefully monitored and controlled for the subsequent stages of the GTL process.
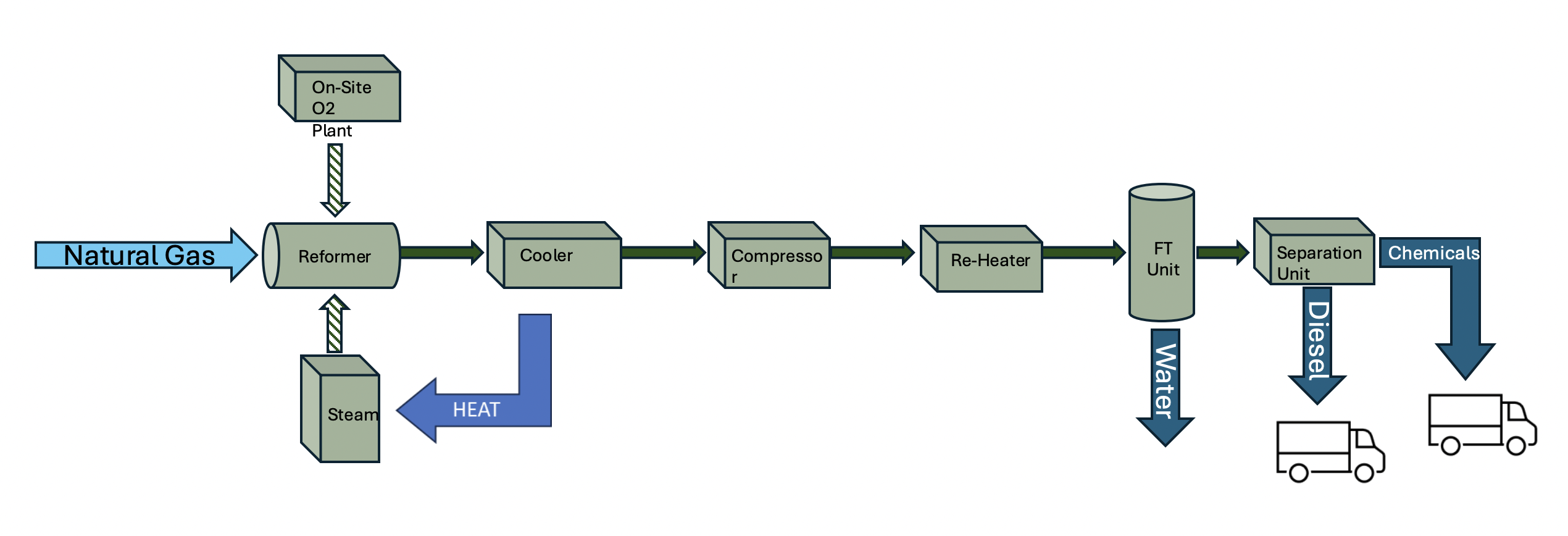
GTL Process Overview:
- Initial Reforming Stage: The G-Reformer® begins by converting natural gas into a mixture of 2 parts hydrogen and 1 part carbon monoxide (SYNGAS). This initial stage sets the foundation for the subsequent processes.
- Cooling and Compression Stage: After leaving the G-Reformer®, the SYNGAS is cooled, and the captured heat is repurposed for other plant functions, such as steam generation. The SYNGAS is then compressed and reheated for input into the Fischer-Tropsch (FT) unit.
- Fischer-Tropsch (FT) Stage: The FT unit is a well-established technology that converts SYNGAS into liquid products based on the unit’s design and catalyst used. GWTI has developed a specific catalyst tailored for GTL applications. This stage converts the SYNGAS into a liquid that contains high-purity “tech-grade” water and a mixture of organic chemicals, including a high-cetane diesel blend stock, which can be partially converted to jet fuel blend stock. Unlike other GTL processes, GWTI’s design eliminates waxes in the output. The diesel/jet fuel blend stock is highly pure because it is derived from natural gas rather than refined from crude oil. It is ideal for blending with lower-grade fuels to improve cetane (or equivalent jet fuel) ratings) and meet air quality standards.
- Separation Stage: The liquid is separated into various components after leaving the FT unit. The water and associated alcohols are separated, and the water-borne alcohols are removed, leaving ultra-pure “tech water.” The remaining chemicals are then separated from the remaining mixture. The separated output produced is highly pure, making it valuable in various industries. Currently imported from China and refined from crude oil, these chemicals can be produced domestically with superior purity using GWTI’s GTL process. The liquid products can be separated on-site using separation towers, but GWTI recommends further output processing at a specialized separation system elsewhere.
Environmental and Economic Benefits: The GTL process creates extremely low airborne carbon emissions, as virtually all carbon is embedded in the produced liquid hydrocarbon chemicals. Benefits include eliminating flaring or venting natural gas in oil production, monetizing stranded natural gas, and eliminating leaking natural gas from decommissioned or capped oil wells or coal mines. Renewable natural gas can also be used as input for this GTL process resulting in “green” versions of the outputs. The GTL process provides an attractive monetization alternative to other natural gas uses and a rapid return on investment.