Gas to Methanol Plant Details
Overview of the Gas-to-Methanol (GTM) Process
A Gas-to-Methanol (GTM) plant is designed to convert natural gas into methanol, a versatile and easily transportable liquid fuel. The operation of a GTM plant requires key inputs: pipeline-quality natural gas, 90% purity oxygen (O2), clean water, and electricity. Given the variability in site conditions, conducting a site survey by an EPC (Engineering, Procurement, and Construction) firm is a recommended first step for those considering building a GTM plant.
Input Requirements:
- Pipeline Quality Natural Gas: The natural gas supply can come from various sources, such as a pipeline, a commercial gas supplier, a renewable gas source, or directly from a gas well, provided the gas meets specified quality standards. The G-Reformer® console continuously monitors the composition of the input gas in real-time, which is especially critical for non-commercial gas sources. Pre-treatment may not be necessary if the gas falls within the acceptable range for sulfur compounds as found in commercial natural gas. For well-head gas, a certified fuel sample analysis is crucial to determine its suitability, and in some cases, more energetic gases can enhance production efficiency.
- Oxygen: The plant requires 90% purity oxygen. For a single G-Reformer® system, liquid oxygen (LOX) delivered from a local supplier can eliminate the need for on-site oxygen generation. However, an on-site oxygen concentration plant will be necessary for larger plants (more than one G-Reformer®) or plants in locations where delivered oxygen is not an option. This technology, commonly sourced from specialty vendors, becomes more economically efficient as plant size increases.
- Clean Water: Essential for the methanol production process.
- Electricity: Required to power the GTM plant operations. Options exist to co-generate electricity where grid power is unavailable.G-Reformer® System: The G-Reformer® system is controlled via a custom-built control console developed by GWTI. This console enables remote monitoring and control, including monitoring natural gas input composition and initiating system shutdown if necessary. The G-Reformer® produces a mixture of hydrogen and carbon monoxide, known as SYNGAS, which is carefully monitored and controlled for subsequent stages of the GTM process.
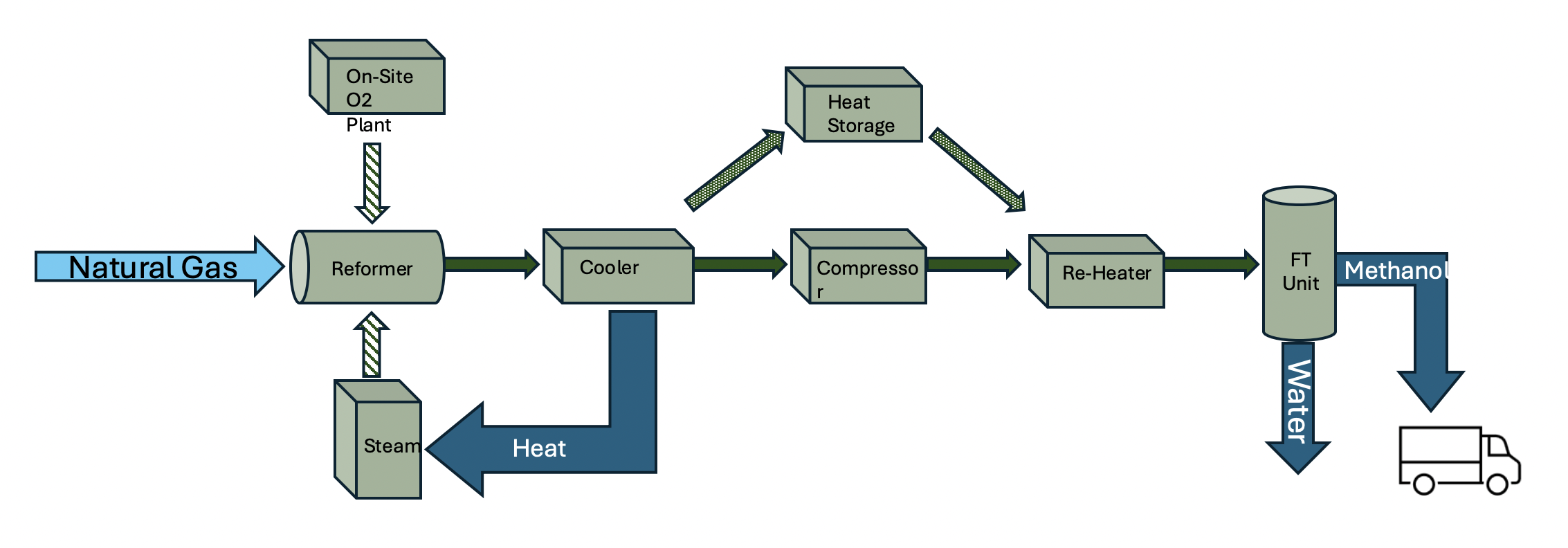
G-Reformer® System: The G-Reformer® system is controlled via a custom-built control console developed by GWTI. This console enables remote monitoring and control, including monitoring natural gas input composition and initiating system shutdown if necessary. The G-Reformer® produces a mixture of 2 parts hydrogen and 1 part carbon monoxide, known as SYNGAS, which is carefully monitored and controlled for subsequent stages of the GTM process.
GTL Process Overview:
- Initial Reforming Stage: The G-Reformer® begins by converting natural gas into a mixture of hydrogen and carbon monoxide. This initial stage sets the foundation for the subsequent processes.
- Cooling and Compression Stage: After leaving the G-Reformer®, the SYNGAS is cooled, and the excess captured heat is repurposed for other plant functions, such as steam generation. The SYNGAS is then compressed and reheated for input into the Fischer-Tropsch (FT) unit.
- Fischer-Tropsch (FT) Stage: Fischer-Tropsch (FT) Unit: Using a catalyst identified by GWTI as suitable for methanol production, the FT unit converts SYNGAS into methanol. This stage produces methanol and a small quantity of pure “tech-grade” water. The key objective is to convert natural gas into a transportable liquid fuel, with methanol’s market value significantly higher than natural gas. The methanol produced is highly pure, as it originates from natural gas rather than refined from oil.
Environmental and Economic Benefits: The GTM process creates no airborne carbon emissions, as all carbon is embedded in the produced methanol, a clean-burning hydrocarbon fuel. As a result, the created methanol from “fossil” natural gas input may be graded as “blue” methanol. Additionally, input renewable natural gas will produce “green” methanol, which is considerably more valuable.
The demand for methanol is increasing due to its ease of transportation, stability across various temperature ranges, and ability to remain liquid at atmospheric pressure. Methanol is particularly valuable in remote areas, such as underdeveloped nations, with abundant natural gas but limited access to fuel. Methanol can serve as a clean alternative to wood or other organic fuels for cooking, reducing indoor air pollution and associated health risks. Growing demand for methanol as a fuel and its use as an “anti-freeze” agent in oil and gas production continues to drive increased use of this product.
Innovative Applications: GWTI has researched unique designs for methanol plants, allowing all plant components to be built into storage containers with external connectors. These containerized units can be easily transported and assembled in remote locations, making methanol production feasible in areas where traditional plant construction is impractical. In such cases, methanol could be distributed locally, even in small quantities such as 5-gallon containers, providing essential fuel to isolated communities.